The Ultimate Guide to CNC Prototyping: Everything You Should Know
In today’s fast-moving world of product innovation, CNC prototyping has revolutionized the way engineers and designers bring their ideas to life with exceptional speed and accuracy.
What is CNC Prototyping?
CNC prototyping is the process of utilizing Computer Numerical Control (CNC) machining to fabricate functional prototypes from various materials with high precision and consistency.
Key Aspects of CNC Prototyping:
- Definition: CNC prototyping refers to creating prototypes using automated machining processes controlled by computer programs.
- Comparison with Other Prototyping Methods: It differs from 3D printing and injection molding in terms of material versatility, precision, and application.
- Significance in Manufacturing: CNC prototyping plays a vital role in modern production by ensuring accuracy, efficiency, and adaptability for diverse industries.
How CNC Prototyping Works
CNC prototyping converts digital designs into tangible models using automated machining tools governed by specialized software.
CNC Prototyping Process Overview:
- Understanding the CNC Workflow: The process begins with a digital CAD design, which is then translated into machine instructions (G-code).
- Types of CNC Machines: Includes CNC mills, lathes, routers, and multi-axis machines, each suited for different prototyping needs.
- Step-by-Step Guide: Designing the model → Generating machine code → Material selection → Machining process → Post-processing and finishing.
Materials Used in CNC Prototyping
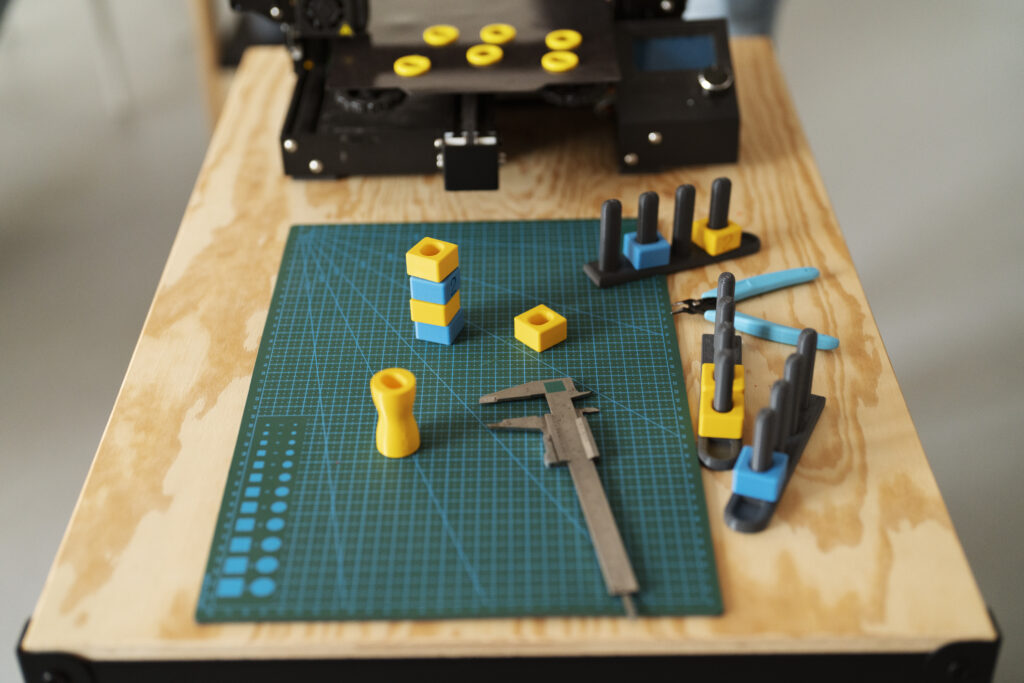
Choosing the right material is crucial as it directly impacts the prototype’s durability, functionality, and performance.
Commonly Used Materials:
Metals:
- Aluminum – Lightweight and corrosion-resistant.
- Stainless Steel – Strong and durable for high-stress applications.
- Titanium – Excellent strength-to-weight ratio.
- Brass – Good machinability and electrical conductivity.
Plastics:
- ABS – Affordable and impact-resistant.
- Polycarbonate – High toughness and transparency.
- Nylon – Strong, flexible, and wear-resistant.
- PEEK – Heat and chemical resistant.
Composites & Other Materials:
- Carbon Fiber – Lightweight with high strength.
- Foam – Used for lightweight modeling.
- Wood – Suitable for aesthetic prototypes.
Advantages of CNC Prototyping
CNC prototyping is widely preferred due to its numerous benefits, including:
- Unmatched Precision & Accuracy – Ideal for intricate and high-tolerance parts.
- Versatility in Material Selection – Supports a wide range of metals, plastics, and composites.
- Scalability – Suitable for both low and high-volume production.
- Faster Turnaround Time – More efficient than traditional manufacturing methods.
- Cost-Effectiveness – Reduces long-term expenses through durability and reliability.
Limitations of CNC Prototyping
Despite its advantages, there are certain drawbacks to consider:
- Higher Initial Setup Costs – Expensive machinery and setup requirements.
- Material Wastage – Subtractive manufacturing leads to excess material removal.
- Design Complexity Constraints – Intricate designs may require multi-axis CNC machines, increasing costs.
CNC Prototyping vs. 3D Printing: Choosing the Right Method
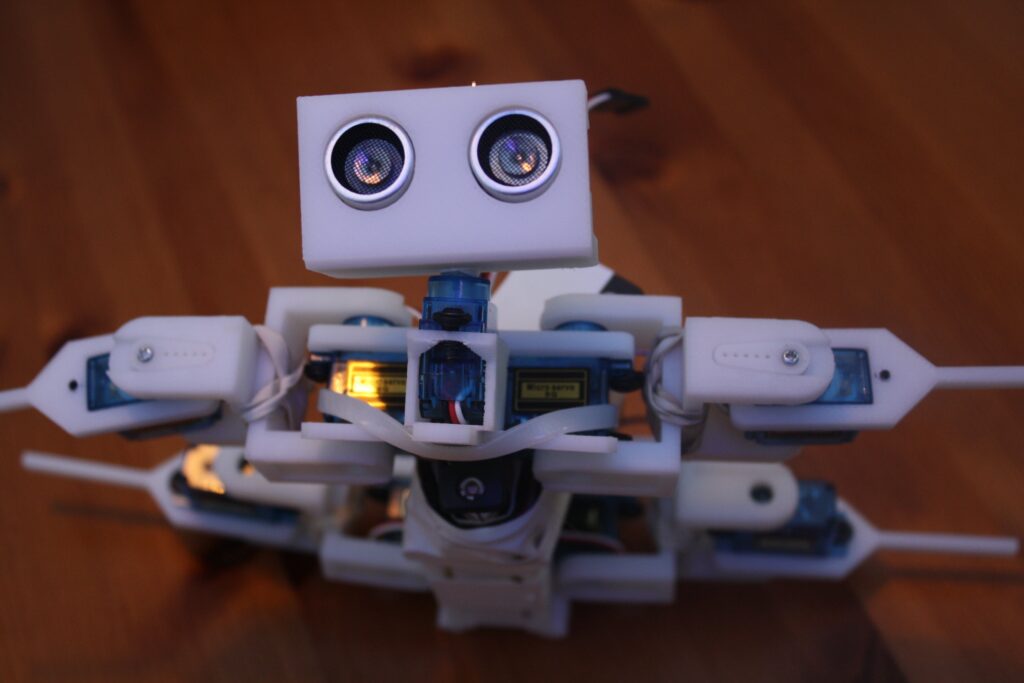
Both CNC prototyping and 3D printing serve as effective prototyping methods, but they differ significantly in terms of application. For a more detailed breakdown of these differences, you can check out Fictiv’s CNC vs 3D Printing comparison guide which highlights the pros and cons of each process based on real-world use cases.
Feature | CNC Prototyping | 3D Printing |
---|---|---|
Accuracy | High | Moderate to High |
Material Options | Extensive (metals, plastics, composites) | Limited (plastics, resins, some metals) |
Production Speed | Faster for bulk production | Faster for single prototypes |
Cost Efficiency | Higher cost for low-volume runs | Lower cost for low-volume runs |
Surface Finish | Smooth with minimal post-processing | Requires post-processing for refinement |
Cost Breakdown: What Affects CNC Prototyping Expenses?
Several factors influence the overall cost of CNC prototyping. A helpful resource to explore estimated costs and influencing factors is RapidDirect’s CNC machining pricing guide.
Cost Components:
Material Selection – Some materials, like titanium, are more expensive than plastics.
Machine Setup Fees – Initial programming and calibration add to costs.
Labor Costs – Skilled CNC machinists may be required for complex designs.
Post-Processing & Finishing – Surface treatment and polishing increase expenses.
Estimated Pricing:
CNC Prototype Type | Approximate Cost |
---|---|
Basic Prototype (Plastic, Simple Design) | $50 – $200 |
Standard Prototype (Metal, Moderate Complexity) | $200 – $800 |
High-Precision Prototype (Titanium, Complex Design) | $800 – $5,000+ |
Best Practices for CNC Prototyping
To enhance efficiency and cost-effectiveness, consider these best practices:
Optimize Design for Manufacturability (DFM) – Ensure the design is feasible for CNC machining. Protolabs’ DFM tips are a great starting point.
Select the Right Material – Match material properties to the prototype’s purpose.
Work with Skilled Machinists – Expertise helps in optimizing precision and efficiency.
Minimize Unnecessary Complexity – Simplifying design reduces machining time and cost.
Plan for Post-Processing – Consider finishing techniques for better aesthetics and functionality.
How to Choose a CNC Prototyping Service
Selecting a reputable CNC prototyping service ensures high-quality results and timely delivery. If you’re unsure where to start, Xometry’s CNC service overview can give you a sense of what to look for in a provider.
Key Factors to Evaluate:
Industry Experience – Choose a provider with expertise in CNC machining.
Material & Machine Availability – Ensure they offer a variety of materials and advanced machines.
Turnaround Time – Fast service ensures quicker project completion.
Pricing & Transparency – Look for competitive pricing with no hidden fees.
Customer Reviews & Testimonials – Research user feedback before selecting a service.
Final Thoughts on CNC Prototyping
CNC prototyping continues to be a fundamental aspect of modern product development, providing a reliable method to transition from concept to production with high precision.
Key Takeaways:
CNC machining is ideal for precise, durable prototypes.
The right material and design optimization significantly impact cost and performance.
CNC prototyping remains a crucial tool for industries ranging from automotive to aerospace.
Future Trends:
AI and automation advancements in CNC machining.
Improved material efficiency and sustainability.
Integration of CNC machining with hybrid manufacturing techniques. For a glimpse into what’s coming, Tech Briefs outlines future trends in CNC machining.
Frequently Asked Questions (FAQs)
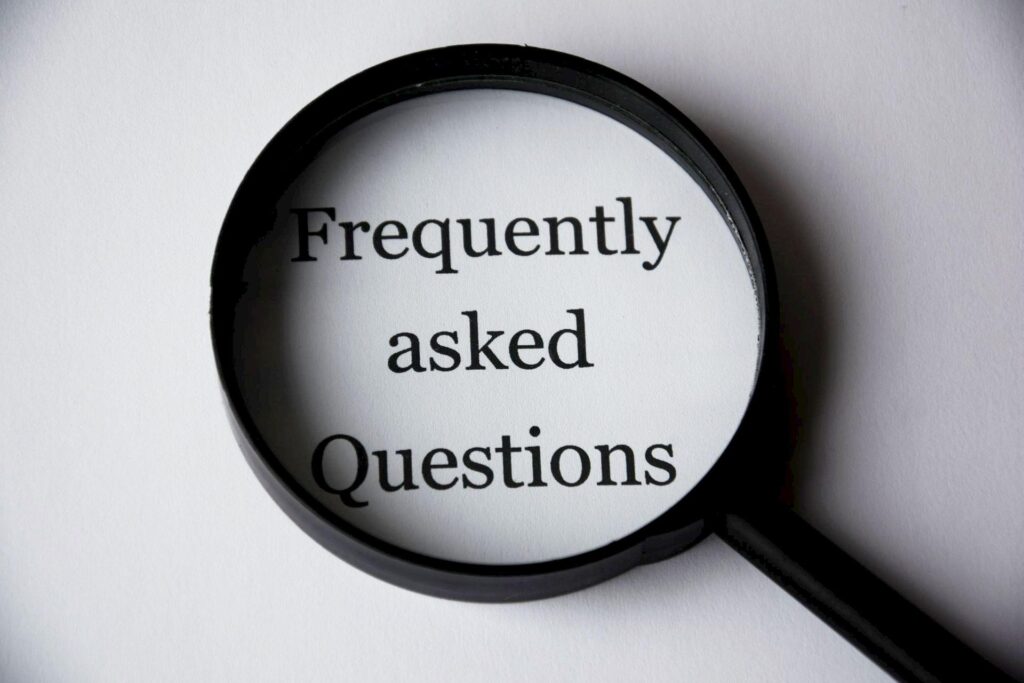
1. How long does CNC prototyping take?
The lead time varies based on complexity and material but typically ranges from a few days to a couple of weeks.
2. Can CNC prototyping be used for large-scale production?
While primarily used for low-volume production, CNC machining can handle high-precision mass manufacturing.
3. What is the best material for CNC prototyping?
The ideal material depends on the prototype’s purpose. Aluminum is great for durability, while ABS is cost-effective for lightweight applications.
4. How does CNC prototyping compare to injection molding?
CNC prototyping is faster for small-batch production and allows for flexible design changes, whereas injection molding is better suited for high-volume manufacturing.
5. Is CNC prototyping environmentally friendly?
Although CNC machining generates waste, the materials used are often recyclable, making it a more sustainable option than some alternative methods.
By utilizing CNC prototyping effectively, businesses can streamline product development and bring innovative ideas to market with efficiency and precision.